The ring gear changed from the A to 4A Roadsters. The difference is the number of teeth on the ring gear as well as the on the starter gear. Keep this in mind and only use A series ring gear with A series starters.
That being said, I was in the enviable position of having TWO flywheel/ring gear. One nice flywheel had an awful ring gear. The other had a questionable flywheel and a nice ring gear. What to do... what to do... Got it! I will swap them over!
The ring gear are shrunk on the flywheel. That is that it held in place simply by the inside of the ring gear being smaller in diameter than the outside of the flywheel. How does this happen? Well to install the gear, it must be heated which allows the metal to expand and the inside diameter increases. To help matters along for installation, the flywheel can be cooled which causes the metal to shrink. Place the expanded (and hot) gear on the shrunk (and cold) flywheel and let nature/physics take their course.
The end result is a ring gear that is held tightly in place and can be replaced should it become worn.
Thursday, June 01, 2006
Part 13 - Pipe up!


The engine that I am rebuilding came with a perfectly good petrol pipe. It also came with an unknown Solex carb. The pipe was definitely made to fit the carb option. My setup features a SU Down draft (see Part 12) so there were a few issues to deal with. First was that the pipe was a bit too short, the other was the carb connector. I wanted to use the banjo connector that was originally with this carb. I think that they are cool, and for that reason I will take the hours and hours to painfully reconstruct a new pipe. Actually it too less than 20 minutes from start to finish, but do not tell anyone.
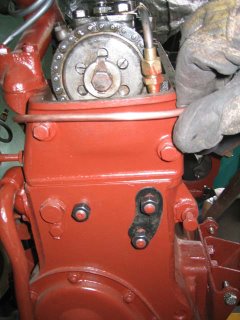
I started by straightening a piece of coiled copper pipe. Copper is great because it is able to take a bend rather easily. This also means that care must be exercised so as not to kink the pipe.. Being the ever nit picker, I evened out the bumps by rolling it on the floor of the garage under a piece of ply. If you have ever made snakes out of clay as a kid, you see what I did. No measuring yet, but I did make sure that the pipe was definitely long enough.
Then I made the fitting for the pump-end of the pipe and attached it to the petrol pump. From there I gently bent and curved the pipe to follow the ins and outs as well as the ups and downs and the spins to follow the curves of the engine. I used the original pipe as a guide especially to see where the pipe passed under the lower water manifold and around the breather tube.



Then another bend to bring the pipe up to the carb. With the banjo in place, the bend was made and then the pipe measured for cutting.
Again a fitting session with the banjo in place and the pipe inserted. Any final adjustments can be made to the length of the pipe.

A pass or two with some steel wool was just the trick to make it look nice.
Getting closer!
Subscribe to:
Posts (Atom)